In jewelry making, two prominent techniques vie for attention: PVD coating vs electroplating. Both methods offer unique advantages and considerations, influencing the quality, durabilité, and aesthetic appeal of the final product. Understanding the intricacies of each technique is essential for jewelry artisans and enthusiasts alike. Let’s delve into a comprehensive comparison to discern the nuances between PVD coating and electroplating.
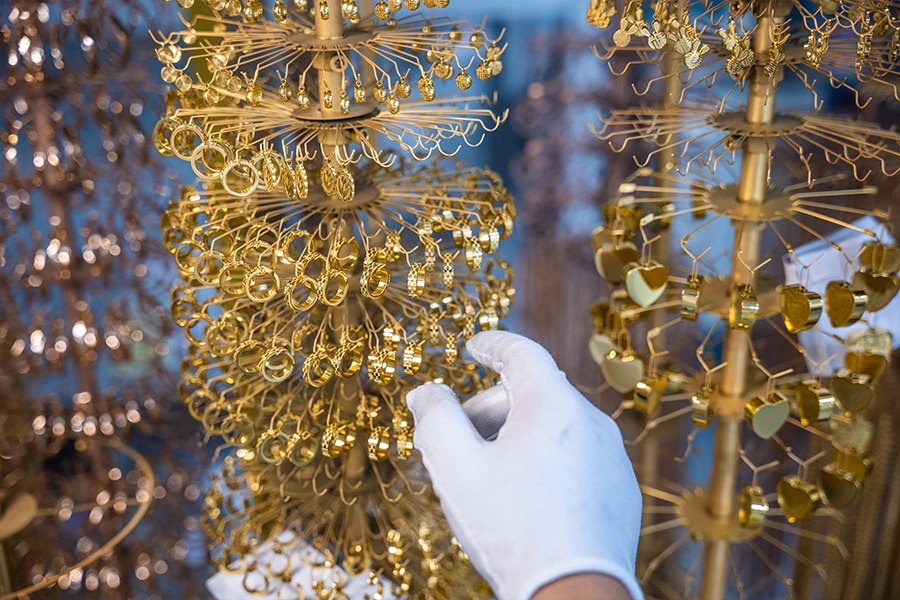
What Is PVD Coating?
PVD, or Physical Vapor Deposition, coating is a sophisticated process that involves depositing thin layers of materials onto surfaces through a vacuum environment. Unlike traditional coating methods, PVD coating operates at the atomic level, ensuring exceptional adhesion and uniformity. This technique utilizes high-energy sources, such as plasma or arc evaporation, to vaporize solid materials into a gaseous state. The vaporized particles then condense on the substrate, forming a durable coating with enhanced properties.
Process of PVD Coating
The process of PVD coating in jewelry making involves several meticulous steps to apply thin layers of material onto jewelry substrates in a vacuum environment. Here’s a detailed overview of the PVD coating process specifically tailored for jewelry production:
- Cleaning and Preparation of Jewelry: The jewelry pieces undergo thorough cleaning and preparation to remove any dirt, huiles, or residues that could impair adhesion. This step is crucial for ensuring proper bonding between the jewelry surface and the deposited coating.
- Fixturing and Placement in Vacuum Chamber: The cleaned jewelry pieces are carefully fixtured and placed inside a vacuum chamber designed for PVD coating. Proper fixturing ensures even coating deposition and minimizes handling-induced contamination. The vacuum chamber is then evacuated to create a low-pressure environment, typically below atmospheric pressure.
- Surface Activation and Cleaning: Prior to coating deposition, the jewelry surfaces may undergo surface activation and cleaning processes to enhance adhesion. This may involve ion bombardment or plasma cleaning to remove surface contaminants and promote surface roughness, improving the substrate’s receptivity to the coating material.
- Material Deposition: The coating material, often in the form of a solid target or source, is vaporized using high-energy sources such as electron beams, sputtering targets, or arc evaporation. The vaporized material then condenses onto the jewelry surfaces, forming a thin film or coating layer. This deposition process occurs in a controlled manner within the vacuum environment to ensure uniform coverage and adherence to the jewelry substrates.
- Controlled Thickness and Composition: The thickness and composition of the deposited coating are carefully controlled by adjusting process parameters such as deposition rate, substrate temperature, and deposition time. This precision control ensures consistent coating thickness and desired material properties across all jewelry pieces.
- Post-Coating Treatment (Optional): Depending on the desired properties and aesthetics, the coated jewelry pieces may undergo post-coating treatments such as polishing, buffing, or surface texturing to enhance the appearance and feel of the final product. These treatments can further refine the surface finish and improve the overall quality of the coated jewelry.
- Quality Inspection and Assurance: Once the PVD coating process is complete, the coated jewelry pieces undergo thorough quality inspection and assurance to ensure compliance with specifications and standards. This may include visual inspection, coating thickness measurement, adhesion testing, and assessment of surface finish and appearance.
Types of PVD Coating
PVD coating encompasses a diverse range of techniques, each tailored to specific applications and material requirements. Some common types of PVD coating include:
- Le dépôt physique en phase vapeur (PVD): The general term for the entire process of depositing thin films through vaporization and condensation.
- Cathodic Arc Deposition: Utilizes an electric arc to vaporize solid metal targets, producing dense and adherent coatings.
- Magnetron Sputtering: Involves bombarding a target material with high-energy ions to release vaporized atoms that condense onto the substrate.
- Evaporation Deposition: Evaporates solid materials using resistive heating or electron beams, forming thin films with precise control over thickness and composition.
Pros and Cons of PVD Coating
Here are the advantages and disadvantages of the PVD coating on jewelry.
Avantages:
- Exceptional hardness and wear resistance
- Uniform coating thickness and coverage
- Enhanced adhesion and durability
- Wide range of available materials and finishes
- Environmentally friendly process with minimal waste
Inconvénients:
- High initial investment cost for equipment
- Limited scalability for large-scale production
- The complicated process requires skilled operators.
- Substrate material compatibility may vary.
What Is Electroplating?
Galvanoplastie, also known as electrodeposition, is a widely used technique for applying thin layers of metal onto substrates through electrolysis. This process involves immersing the substrate and a metal electrode in an electrolyte solution, typically containing ions of the desired coating material. When an electric current is applied, metal ions from the electrode dissolve into the electrolyte solution and deposit onto the substrate, forming a thin and uniform coating.
Process of Electroplating
The process of electroplating in jewelry making involves several precise steps to deposit thin layers of metal onto jewelry substrates through electrolysis. Here’s a detailed overview of the electroplating process specifically tailored for jewelry production:
- Cleaning and Preparation of Jewelry: The jewelry pieces undergo meticulous cleaning and preparation to remove any dirt, huiles, or residues that could hinder adhesion. This step is essential for ensuring proper bonding between the jewelry surface and the deposited metal layer.
- Fixturing and Immersion in Electrolyte Solution: The cleaned jewelry pieces are carefully fixtured and immersed in an electrolyte solution containing metal ions of the desired plating material. The jewelry pieces serve as the cathode (negative electrode) in the electroplating cell.
- Selection of Plating Bath: The electrolyte solution, also known as the plating bath, is chosen based on the type of metal to be deposited and the desired properties of the plated layer. Common plating baths include solutions containing metal salts such as gold cyanide, silver nitrate, or nickel sulfate.
- Application of Electric Current: An electric current is applied to the electroplating cell using an external power source. The jewelry pieces serve as the cathode, while an inert metal electrode (such as platinum or titanium) serves as the anode (positive electrode). As the current passes through the solution, metal ions from the anode dissolve into the electrolyte solution.
- Deposition of Metal onto Jewelry Surface: Due to the electric current, metal ions in the electrolyte solution are attracted to the cathode (jewelry substrate) and deposit onto its surface. This results in the formation of a thin layer of metal coating on the jewelry pieces. The thickness of the plated layer can be controlled by adjusting the duration and intensity of the electric current.
- Rinsing and Drying: Once the electroplating process is complete, the plated jewelry pieces are thoroughly rinsed with water to remove any residual electrolyte solution or impurities. They are then carefully dried to prepare for further finishing or post-processing steps.
- Finishing and Polishing (Optional): Depending on the desired aesthetics and properties, the plated jewelry pieces may undergo additional finishing processes such as polishing, buffing, or surface texturing to enhance their appearance and shine. These finishing steps can further refine the surface finish and improve the overall quality of the plated jewelry.
- Quality Inspection and Assurance: After electroplating and any subsequent finishing steps, the plated jewelry pieces undergo thorough quality inspection and assurance to ensure compliance with specifications and standards. This may include visual inspection, thickness measurement, adhesion testing, and assessment of surface finish and appearance.
Types of Electroplating
Electroplating encompasses various methods and materials suited to different applications and desired outcomes. Some common types of electroplating include:
- Nickel Plating: Provides corrosion resistance and decorative appeal to substrates, often used as an undercoat for subsequent plating layers.
- Gold Plating: Imparts a luxurious and durable finish to jewelry, electronics, and decorative items, offering excellent corrosion resistance and aesthetic appeal.
- Silver Plating: Enhances conductivity and tarnish resistance of substrates, commonly used in electronics, tableware, and decorative items.
- Chromium Plating: Delivers exceptional hardness, résistance à la corrosion, et attrait esthétique, ideal for automotive, aerospace, and decorative applications.
Pros and Cons of Electroplating
Here are the advantages and disadvantages of electroplating.
Avantages:
- Versatile process compatible with various substrates
- Cost-effective method for high-volume production
- Precise control over coating thickness and composition
- Wide range of available materials and finishes
- Suitable for complex geometries and intricate designs
Inconvénients:
- Environmental concerns regarding toxic metal ions and waste disposal
- Limited durability compared to PVD coating
- Susceptibility to peeling, flaking, and corrosion over time
- Higher maintenance requirements for plated surfaces
Difference between PVD Coating and Electroplating
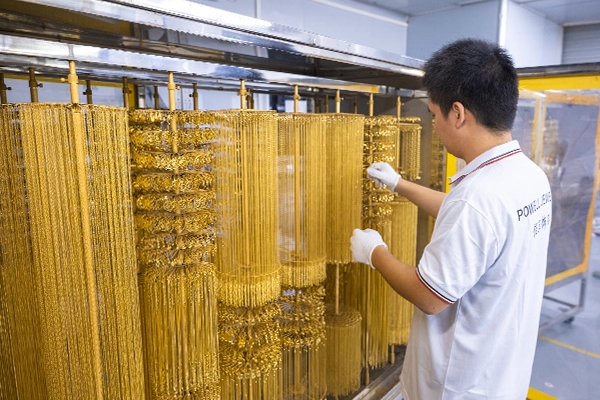
While both PVD coating and electroplating offer viable solutions for enhancing the appearance and properties of jewelry, they differ significantly in terms of process, performance, and application. Here’s a comparison chart outlining the key differences between PVD coating and electroplating:
Aspect | Revêtement PVD | Galvanoplastie |
Processus | Physical vapor deposition in a vacuum environment | Deposition of metal ions through electrolysis |
Mechanism | Vaporization of solid material, condensation on substrate | Dissolution of metal ions in electrolyte solution, deposition on substrate |
Technique | Dissolution of metal ions in an electrolyte solution, deposition on substrate | Thin film deposition at an atomic level |
Equipment | Vacuum chamber, high-energy sources | Electroplating cell, power source, electrolyte solution |
Coating Thickness | Thin, uniform layers | Varies, controlled by current and time |
Material Compatibility | Wide range of materials, including metals, ceramics, polymers | Limited to metals and certain alloys |
Adhesion | Excellent adhesion due to physical bonding | Adhesion depends on surface preparation and process control |
Durabilité | Highly durable, resistant to wear and corrosion | Generally durable, but may be susceptible to wear and corrosion over time |
Aesthetics | Offers various finishes and colors | Limited to metallic finishes and colors |
Impact environnemental | Generally considered environmentally friendly, minimal waste | Concerns regarding waste disposal and toxic metal ions |
Coût | Higher initial investment for equipment | Generally more cost-effective for mass production |
Applications | High-end jewelry, luxury goods, precision components | Decorative items, automotive, electronics, hardware |
Entretien | Minimal maintenance required | Regular maintenance may be needed to preserve appearance |
Revêtement PVD vs galvanoplastie: Which Is Better for Jewelry Making?
The choice between PVD coating and electroplating ultimately depends on the specific requirements of the jewelry piece, including design, functionality, and budget constraints.
PVD coating excels in delivering superior durability, wear resistance, et attrait esthétique, making it suitable for premium jewelry brands and high-end accessories.
Conversely, excellent electroplating offers a more cost-effective solution for producing large quantities of jewelry with decorative finishes and moderate durability.
Donc, you should evaluate the desired attributes and performance criteria first. Stainless steel jewelry makers like Jusnova can select the most suitable coating technique to achieve your creative vision and meet market demands.
Conclusion
In the competitive landscape of jewelry making, selecting the appropriate coating technique is pivotal in defining the excellence, longevity, and allure of the end product. The comparison between PVD coating and electroplating presents two distinct methodologies, each presenting unique advantages and constraints. PVD coating showcases unmatched durability and performance, particularly suited for crafting luxury jewelry pieces. Conversely, electroplating offers versatility and cost-effectiveness, ideal for mass production and decorative applications. By comprehending the nuances of PVD coating vs electroplating and discerning their respective merits, jewelry artisans can strategically refine their craft, meeting the dynamic demands of consumers in the ever-evolving market.